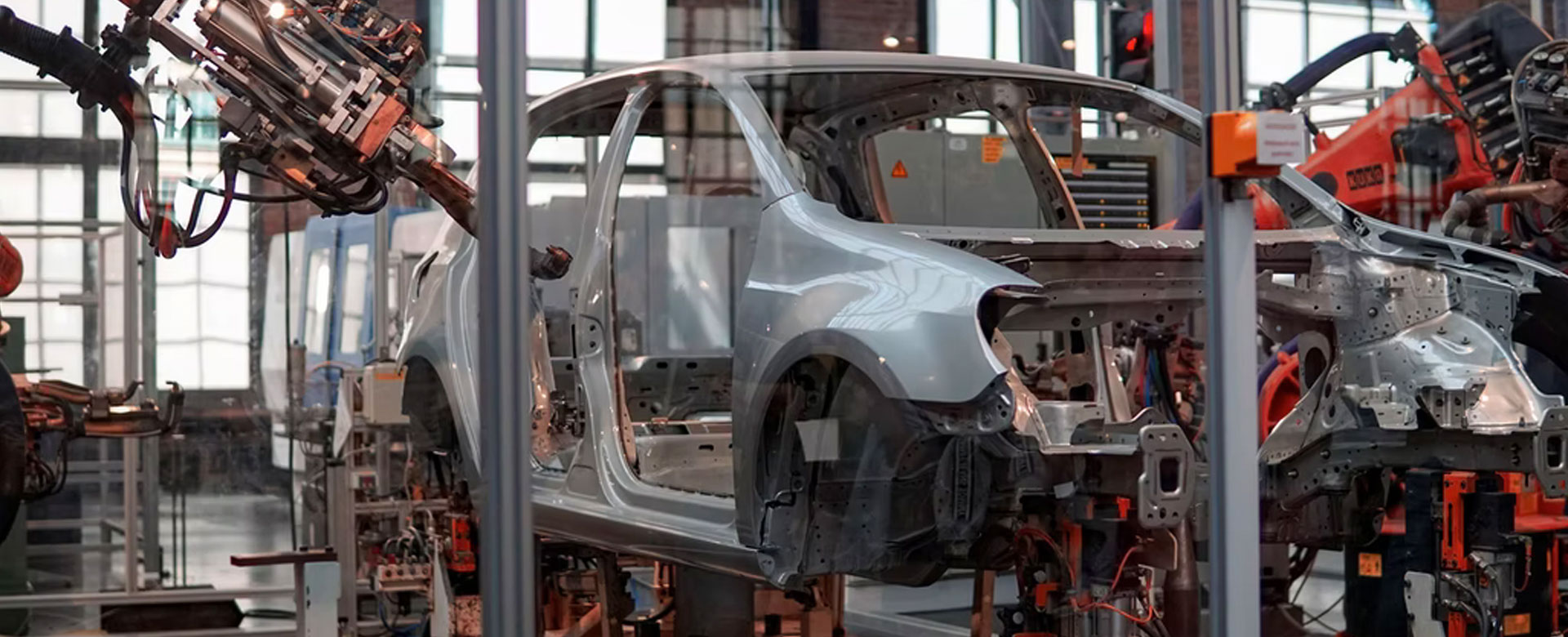
The automotive industry is undergoing a massive disruption – from rising demand for electric cars to autonomous driving and hyper-personalization. However, since the beginning of modern automotive manufacturing, the assembly line has been the heart of every production process.
This linear, static and capital-intensive approach won’t work anymore in the future. Flexible robot concepts allow multifaceted cooperation with the human workforce and enable factories to change their production processes quickly. This is a huge step forward to the future of smart factories and the era of industry 4.0.
A flexible production concept starts with a digital simulation of the car model. This simulation can serve as an early prototype, reducing time-to-market and decreasing research costs. New materials such as carbon fiber can then be used to build early versions of lightweight automobiles or even light trucks.
Human-robot-collaboration/cooperation (HRC) is an essential enabler for agile production concepts in industry 4.0. It combines the best work of both robots and humans – the high precision and payload from robots with humans' cognitive and creative superpower. In such cases, robots usually take over monotonous tasks.
The future of car manufacturing is lean and agile at its heart. Volatile markets and rapidly changing customer demands emphasize the need for a change along the whole supply chain. While an agile production can be a competitive advantage, it also enables new challenger companies to enter the market. New automotive startups can open production facilities using an open ”greenfield” approach while staying independent from venture capital.
ARENA2036 is an excellent case study and research hub for agile car manufacturing. In their own 7,000m2 project space, autonomous guided vehicles (AGVs) transport the components and chassis from workstation to workstation to decrease the dependence on traditional manufacturing lines. AGVs are lightweight robots and serve as a cyber physical system, allowing a flexible chain of assembly stations.
In this scenario, each assembly station can be easily adapted to the changing needs of the production. New variants and hyper-personalized components can be assembled without the need of rebuilding the whole production line. Imagine customers choosing a unique combination of materials and colors at scale.
AGVs and other kinds of collaborative robots can use different tools based on their current task and move freely in the production halls. That enables factories to change the layout or positioning of stations quickly. It also makes the factory more scalable by leveraging small lot sizes. For medium lot sizes, an increasing percentage of human-robot-collaboration/cooperation can be used, and in case of large lot sizes, parallel, linear assembly lines can be used.
Agile production systems demand fenceless robotic automation without decreasing the safety of the humans collaborating with the robots. AIRSKIN® is a patented, add-on safety sensor solution for robots, AGVs, and other moving machinery. This enables true fenceless robotic automation and allows automotive manufacturers to shorten the product life cycle times while opening the possibility of personalized and more innovative products.