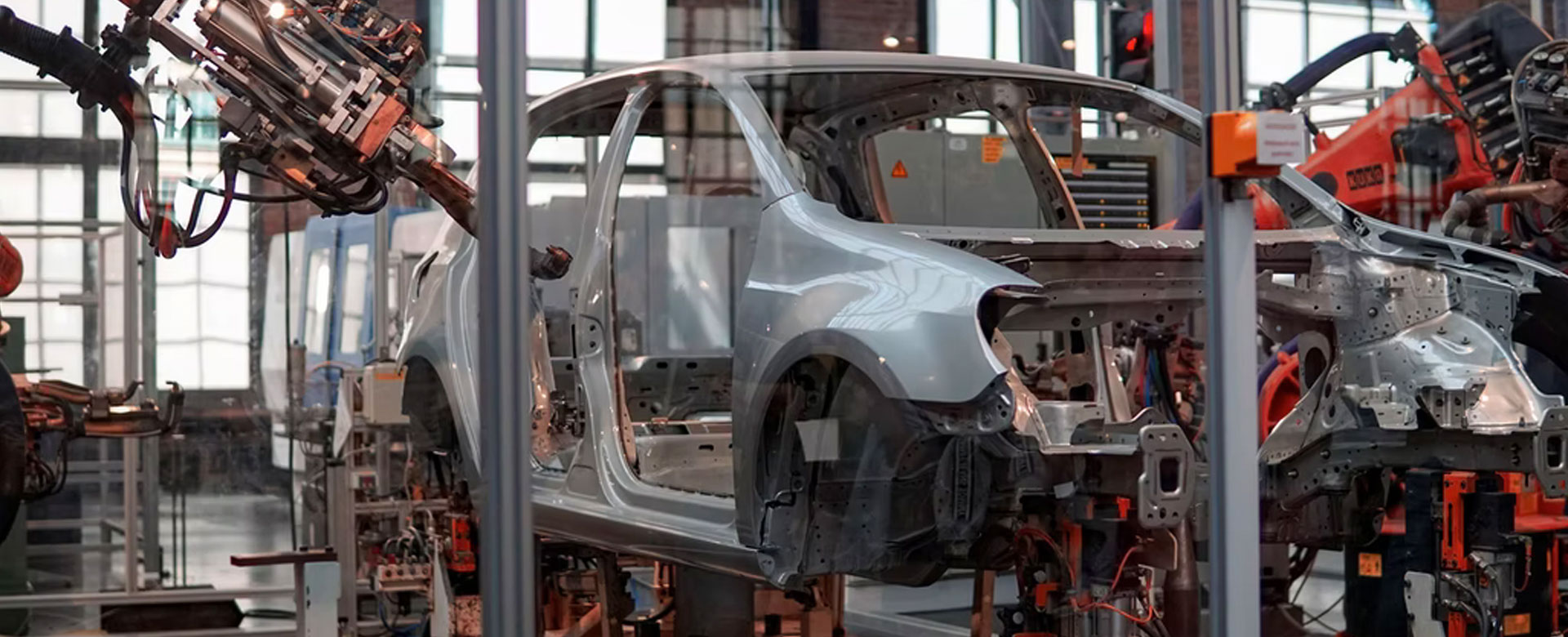
Die Automobilindustrie befindet sich in einem massiven Umbruch - von der steigenden Nachfrage nach Elektroautos über autonomes Fahren bis hin zur Hyperpersonalisierung. Doch seit den Anfängen der modernen Automobilproduktion ist das Fließband das Herzstück jedes Produktionsprozesses.
Dieser lineare, statische und kapitalintensive Ansatz wird in Zukunft nicht mehr funktionieren. Flexible Roboterkonzepte ermöglichen eine vielseitige Zusammenarbeit mit der menschlichen Belegschaft und versetzen Fabriken in die Lage, ihre Produktionsprozesse schnell zu ändern. Das ist ein großer Schritt in die Zukunft der Smart Factories und in das Zeitalter der Industrie 4.0.
Ein flexibles Produktionskonzept beginnt mit einer digitalen Simulation des Fahrzeugmodells. Diese Simulation kann als früher Prototyp dienen, was die Time-To-Market verkürzt und die Forschungskosten senkt. Neue Materialien wie Karbonfasern können dann verwendet werden, um frühe Versionen von leichten Automobilen oder sogar leichten Lastwagen zu bauen.
Die Human-Robot-Collaboration/Cooperation (HRC) ist ein wesentlicher Wegbereiter für agile Produktionskonzepte in der Industrie 4.0. Sie kombiniert die besten Fähigkeiten von Robotern und Menschen – die hohe Präzision und Nutzlast von Robotern mit der kognitiven und kreativen Superpower des Menschen. In solchen Fällen übernehmen Roboter meist monotone Aufgaben.
Die Zukunft der Automobilproduktion ist im Kern schlank und agil. Volatile Märkte und sich schnell ändernde Kundenwünsche machen einen Wandel entlang der gesamten Lieferkette notwendig. Eine agile Produktion kann nicht nur ein Wettbewerbsvorteil sein, sondern ermöglicht auch den Markteintritt neuer Wettbewerber. Startups in der Automobilindustrie können Produktionsanlagen in kürzester Zeit eröffnen und dabei unabhängig von Risikokapital bleiben.
ARENA2036 ist eine hervorragende Fallstudie und ein Forschungszentrum für die agile Automobilproduktion. In ihrem eigenen 7.000 m2 großen Projektraum transportieren autonome fahrerlose Transportsysteme (AGVs) die Komponenten und Fahrgestelle von Arbeitsplatz zu Arbeitsplatz, um die Abhängigkeit von den traditionellen Fertigungsstraßen zu verringern. AGVs sind leichte Roboter und dienen als cyberphysikalisches System, das eine flexible Kette von Montagestationen ermöglicht.
In diesem Szenario kann jede Montagestation leicht an die wechselnden Anforderungen der Produktion angepasst werden. Neue Varianten und hyper-personalisierte Komponenten können montiert werden, ohne dass die gesamte Produktionslinie umgebaut werden muss. Kunden können beispielsweise einzigartige Kombinationen von Materialien und Farben wählen – und das skalierbar!
AGVs und andere Arten von kollaborativen Robotern können je nach ihrer aktuellen Aufgabe unterschiedliche Werkzeuge verwenden und sich frei in den Produktionshallen bewegen. So können Fabriken das Layout oder die Positionierung von Stationen schnell ändern. Außerdem wird die Skalierbarkeit der Fabrik durch die Nutzung kleiner Losgrößen erhöht. Bei mittleren Losgrößen kann ein zunehmender Prozentsatz an Mensch-Roboter-Kollaboration eingesetzt werden, und bei großen Losgrößen können parallele, lineare Montagelinien verwendet werden.
Agile Produktionssysteme erfordern eine zaunlose Roboterautomatisierung, ohne die Sicherheit der Menschen, die mit den Robotern zusammenarbeiten, zu beeinträchtigen. AIRSKIN® ist eine patentierte, zusätzliche Sicherheitssensorlösung für Roboter, AGVs und andere bewegliche Maschinen. Das ermöglicht eine zaunlose Roboterautomatisierung und unterstützt somit Automobilhersteller dabei, die Produktlebenszykluszeiten zu verkürzen und gleichzeitig die Herstellung personalisierter und innovativerer Produkte umzusetzen.