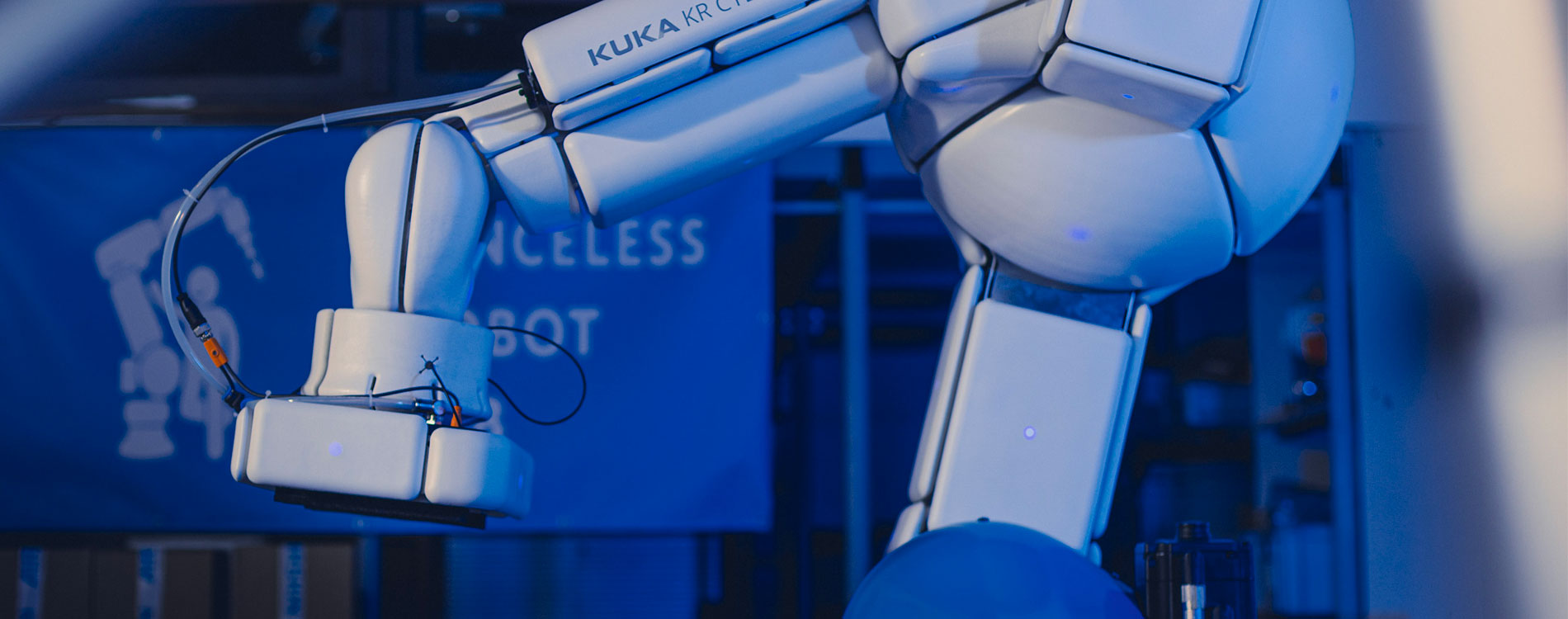
Looking at the visions and predictions for tomorrow’s productions, one cannot fail to recognize that one part is missing that is integral for today's factories: fences and barriers separating humans and robots. Almost all global players in manufacturing have corporate visions that show open, flexible, and robust production layouts that enable mass customization. But these visions are only possible if fencelessness does not come at the cost of productivity.
From the very beginning, robots have been enclosed in cages or other safety barriers to protect workers from possible injuries. Although this type of robot, commonly referred to as simply “industrial robot”, is still widely installed today, there is an increasing trend toward what is known as collaborative robotics.
Collaborative robots, short “cobots”, are called this way because of their possible use in collaborative applications. “Fenceless robots” is a term used to describe robots not enclosed in cages or other safety barriers but not predominantly built for collaboration.
Over the past couple of years, there has been a trend toward installing more and more cobots. The share of cobots has been growing in the last few years. Especially in 2021, there is an estimated massive jump in annual installations of cobots.
One of the most significant advantages of using a cobot is that they are much safer to work with than traditional industrial robots. This is because they are designed to work closely with humans and have built-in safety features that prevent them from harming people.
However, looking at the real motivation for investing in cobots, it becomes clear that companies aim for fencelessness, not collaboration per se. It is estimated that fewer than 5% demand an actual collaborative use, while fenceless applications account for approximately 70% of the demand for cobots.
Fenceless robots are attractive because they save floor space, offer flexibility between workplaces and enable production sites to use an open layout while keeping all the trusted benefits of industrial robots.
In the automotive industry, for example, the use of a fenceless setup is growing because it offers the possibility of having a completely flexible and reconfigurable production line. This is especially important as car manufacturers constantly introduce new models and variants.
A cobot is simply a robot designed to work closely with humans and collaborate with them. This means that cobots usually have to be much smaller and lighter than traditional industrial robots, so they can move faster without exceeding the maximum permissible forces on impact. They use a smooth outer shape to prevent clamping and shearing and safety sensors to enable a safe working environment. In most cases, they are also easy to use and set up without necessary knowledge about the system.
To use robots or cobots without fences, a technical safety solution is needed. While traditionally, these were light curtains, laser scanners or floor mats, cobots use power and force limitation to limit forces and pressures exerted on the human body during contact to safe levels.
There are a variety of safety solutions based on contacts, such as mechanical switches, torque sensors or piezo-resistive foils. AIRSKIN® uses air pressure sensors inside soft air-tight pads to very sensitively detect contact-based pressure changes resulting from the deformation of the pads. The soft surface spreads contact forces, and the cushioning effect dissipates energy during collisions, reducing forces and pressures and enabling higher permissible speeds.
When comparing cobots to AIRSKIN®, multiple benefits can be observed, resulting in higher speed and flexibility and more space and safety.
Cobots |
AIRSKIN® |
Reacts after critical force reached |
Reacts before critical force reached |
Hard shell means small contact area |
Soft shell means large contact area |
Low masses are necessary to keep forces low |
High masses are possible |
In conclusion, the development of fenceless robotics is driven by the advantages they offer. These advantages include saving floor space, flexibility between workplaces and improved safety. As the technology develops, the number of applications for fenceless robotics will likely increase.
Learn more about the current and future technologies behind fenceless and collaborative robotics and how AIRSKIN® positions itself in the race for the future of production. During the webinar, we also answered individual questions.